Introduction
Press tool design is an integral part of the mold-making process and one that will help determine how well your plastic parts come out. Here are some of the basic elements to consider when designing press tools for your molds.
Press tool design and production may sound intimidating, but it’s not something that should scare you. In fact, it’s an important skill to learn if you want to continue growing as a designer and producing high-quality parts. That’s why we’ve put together this overview of press tool design and production that can help you understand this process so you can produce excellent parts every time!
Press Tool Design Components
The major press tool die components are the punch and the die holder which help in fixing the die to the press machine. With regard to the manufacturing processes of press tools, it is necessary to utilize three main manufacturing methods: stamping/coining (sheet metal pressing), machining (metal shaping by using rotating cutting tools like mills or lathes), and wire-cut EDM (Electrical Discharge Machining). For the manufacture of special parts – rotor discs for axial turbines – you can apply other types of moldings with limited dimensional tolerances as well as the use of plasma spraying or powder metallurgy.

Press Tool Adjustment
Backing plates, punch plates and adjusting the height of the die are all important aspects of your tools. It is quite common for press tooling to work at extreme angles and that’s why backing plates and punch plates made of cast iron are an industry standard. The material provides a durable, long-lasting backing that can withstand any kind of stress when clamped down. An adjustable-height die allows you to test different depths and clearances without wasting expensive sheet metal punches or time on trial cuts. These features all make for a better-designed tool and ultimately make production more efficient because it cuts down on error and keeps products moving smoothly.
Selection of Materials
The most efficient way to select steel for press tools is to use a computer-controlled process that enables engineers, in a matter of minutes, to review all possible combinations of hardness, yield strength, elongation, tempering treatments, and surface finishes, etc. Thus software will help you sort through such materials as 17-4PH S73400 4140 or 4142 that come in various tempers. The right material selection results in tool life at least twice as long as normal and usually three times longer than typical carbon steels.
Press Tool Efficiency
The accumulation of tool defects in die stamping, also known as punch cracking, occurs through press force and die tool-steel interaction. To minimize punch cracking you need an efficient press tool. This will help reduce excessive punch deflection while reducing tool wear due to crushing between steel punches. The steel type that you use for punch tools needs careful selection because not all types of steel can provide enhanced performance, toughness, and high yield strength, which are essential for effective press tool design. Steel grades that possess a high degree of impact toughness, such as HPM970 or HPM990 (Hitachi Press Steel), will help minimize tool wear by providing increased ductility at low temperatures. This property results in improved fatigue resistance, leading to longer life spans. At higher temperatures, such steels will offer higher impact strengths to resist punch cracking.

Analysis of Punch
A punch is an essential part of a press tool. It performs two functions, cutting and forming when it comes in contact with a material. With all punches, three factors are essential for accurate performance. This is valid or Compound Die, Material Selection, Die Design, Modeling (2D & 3D), Cost Estimation, Analysis of Punch, etc. Punch manufacturers always recommend compound dies to withstand demanding production requirements and to provide cost-effective life cycle costs. To maximize tool life an economic selection of materials are citicial Take into account the hardness, durability, and wear resistance together with minimal distortion or deformation of the material. Designing die to get maximum productivity while maintaining accuracy can also help maximize tool lifetime thus optimizing overall production costs.
What factors should be considered while designing a press tool?
The press tool design, in sheet metal stamping, especially supports the use in large quantities. They are critical for making very high volumes of a component. This press tool is generally made out of larger material, with a higher mass than an ejector die. This material can vary from mild steel, for basic components, to hardened materials for intricately shaped pieces. However, press tools have limitations in their speed of operation due to their size and weight. They also tend to find limitations in their mass production by small batch sizes or huge batches that require additional support structures around them. There are some important factors to consider when designing a press tool. Press tools have a different build depending on what will be their applications.
A few things to keep in mind while designing your press tool are its purpose, shape, and size. These three things should go hand-in-hand as you design your press tool so that it is cost-effective, efficient, and fast. A good rule of thumb for making sure you’re on track with these factors is to ask yourself a simple question. If you were building one hundred parts at once, would you need any kind of support structure? If yes, then chances are your part needs some redesigning before pressing. It’s better to figure out how much material you need now rather than having all your parts break during production. This usually happens because there wasn’t enough room for them in between two plates! To learn more about how we design our tools check out our post How Do We Design Our Tools?
What are the uses of Press tools?
Press tools are used in metalworking (presses) to cut, bend, form, or straighten metal parts. They are created on a press toolmaker machine. Press tools are designed for repetitive production of similar parts and require precise dimensional accuracy, high-pressure capability, and durability. Typical blanking press tools include shear, punch & die(shear dies), notching & piercing(piercing dies). Secondary operations can be performed on some or all of these tools. The main operations include piercing, bending, notching, or piercing but most will require secondary operations to complete a finished part.
Press Tool Applications
Products manufactured using a press can be made from a number of materials. This includes steel, aluminum, brass, magnesium alloy, plastic, rubber, and ceramic. These products find applications in many industries, including automotive, chemical process plants, manufacturing plants of all types; commercial construction; aerospace; military applications; marine or maritime design applications; railroad design applications or nuclear power plants. A press tool is any one of several components that shape material through mechanical force. This force is exerted by a die, impression die, or forming punch. A tool’s surface is often called its face. However, the face also refers to an area that contacts material during piercing operations.
How to choose the right press tools?
Every new project brings a unique set of needs, from the designs to the material used to create it. If you’re looking for new press tools or want your old ones redesigned, choose a manufacturing partner to get there with maximum utilization of manpower and minimize waste. The engineering experts should take your requirements into consideration. They should evaluate what you currently have in place, analyze potential issues, conduct testing and then deliver solutions. This can help them find solutions that fit your needs precisely.
And if you need factory automation systems, you can work with offshore or outsourcing partners! Choose factories that make sure to keep people safe while working on the manufacturing of products. Quality should be their first priority! It’s more than just a mission statement here—it should be the core value system.
The engineers should carefully inspect all products before packaging them for shipping to ensure complete customer satisfaction. Efficient teams work hard to meet every deadline because quality service is as important as great design. Once your product hits store shelves, your press tool manufacturing partner should offer assistance with inventory management. This way you know the number of sales per unit and the location of their deliveries. The sky’s the limit when it comes to custom-designed press tools. Just like their projects, customers’ expectations continue to evolve, but their basic needs remain unchanged: safety, speed, and cost-effectiveness.
The last thing anyone wants is extra costs that come with wasted time. Usually in lieu of time spent producing less-than-optimal results due to faulty equipment. When you outsource production, you can avoid these setbacks. You can do this by ensuring that everyone involved understands your company’s culture and shares its goals. Your team should focus on efficiency rather than profit margins; employees who believe in what they do will produce better results without breaking a sweat.
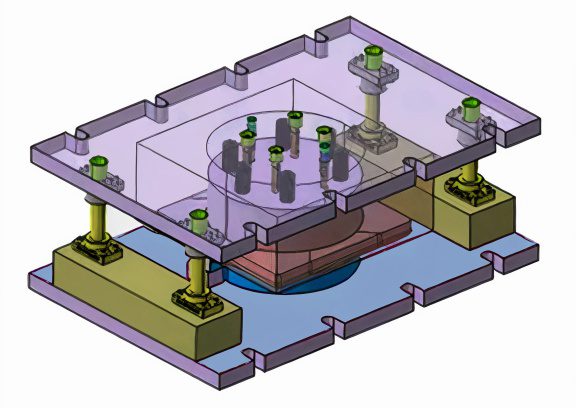
Press tool design Checklist
A well-designed tool has many benefits for your manufacturing process. In press tool design, we can create a variety of options to meet all of your specific requirements, needs, capabilities, and product features.

Contact STAMOD today to speak with an expert about our CNC machining capabilities.
As soon as you have a few sketches on paper or even 3D models from a CAD program, it’s time to start putting together a press tool design checklist. As part of the core service package at STAMOD, we have several cross-functional manufacturing professionals. The team works together in order to complete any job accurately and on time.
Operations – Post mold operation is just one piece of what we do here at STAMOD.
Parts Management – We also offer parts management, complete finish cell operations, supply chain services, and much more.
Quality Check- We make sure to complete every step correctly in order to produce high-quality products on time.
Build Cost Calculation– The first thing to think about when designing a new tool is how much it will cost to build. This may seem like an obvious answer, but not all tools are created equal.
It’s important to consider what each individual component costs because certain components require more labor than others. For example, if you’re making a small die with simple geometry and no special functions, then there’s no need to spend money on specialized tooling. However, if you’re making a large die that requires complex geometry or special inserts for each cavity, then it makes sense to invest in higher-end equipment.
Sum up
Press tool design and production can be tricky business, even with the best of tools, machines, and materials at your disposal. For this reason, it’s important to have an engineer and/or designer on hand who has worked in the industry before and knows what will work best for the job at hand. As one of the premier press tool manufacturers in the country, STAMOD provides you with all of these things in one package. If you need any kind of press tool made in bulk or want to outsource your entire press tool design project , we have customized service models to fit your needs exactly. So please don’t hesitate to get in touch!